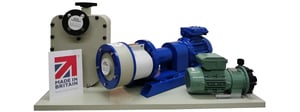
Common Terms Used In The Pump Industry
Common terms used in the pump industry.
Absolute pressure:
The absolute pressure is the sum of the gauge or dial pressure and the atmospheric pressure (14.7psi). If your pump gauge reads 150 psi, then the absolute pressure will be 164.7 psi. Absorbed Power: This is the sum of the hydraulic power (work done by achieving the flow rate and head) and the frictional losses.
Affinity laws:
A set of laws that relate the variables of performance, (impeller shaft speed, head, flow rate) to power, and they are useful to compare the performance of different pumps.
A.P.I. Specifications:
Specifications recommended by the American Petroleum Institute. These specify many safety features of pumps and piping involved in pumping flammable or dangerous substances.
API 610:
A standard used in the petrochemical industry published by the American Petroleum Institute. API 610 ensures that safe, reliable pumps are used in a dangerous industry. ASME: American Society of Mechanical Engineers. Society that promotes the “art, science and practice of multidisciplinary engineering and allied sciences around the globe”.
Atmospheric pressure:
The pressure that the atmosphere exerts, this is measured as the weight of a column of air of a certain cross section and at sea level, the recognised value is 14.7 pounds per square inch (1.03
AVS Standard:
An old, obsolete standard that has been replaced head by the A.N.S.I.standard. The American Voluntary Standard (AVS), was first proposed in the 1950s.
Axial flow pump:
A common type that is essentially an impeller in a pipe. The impeller is driven by an electric motor or petrol/diesel engine, and the propeller’s rotation causes the fluid to be pumped axially along the pipe. The main advantage of this type of pump is that it has a comparatively high discharge at a low head.
Back plate:
Used in some centrifugal pumps. The back plate consists of a gland ring facing the bearing side where the mechanical seal or gland packing's are arranged in such a way that the pumped fluid cannot leak. The other side of the back plate is situated towards the impeller and becomes one of the walls between the suction casing.
Back pull out pump:
A design that allows the entire power end of the pump to be removed for maintenance/replacement while the wet end remains in place.
Back to back double seal:
A mechanical seal configuration typically used when the process fluid is toxic, flammable, or hazardous. This seal is used to prevent the process fluid or its vapour from leaking into the environment.
Back Vane:
Part of the design scheme in impellers used to balance axial thrust on an impeller.
Balance Holes:
Another impeller feature that helps to balance axial thrust and provide lubrication to the seal area located behind the impeller.
Balanced Seal:
The most effective tool to counter heat generation in the stuffing box. The area of the seal face is reduced (i.e. balanced) to reduce the heat generation between the two faces of the seal.
Bar:
Non-SI unit of pressure. Exactly equal to 100,000 Pa. About equal to the atmospheric pressure at sea level.
Barrel Pump:
Used to transfer fluid from a barrel or ICB. Usually available as a separate pump and motor easily assemble by a coarse screw thread and hand wheel.
Barrier fluid/liquid:
The fluid used between the two mechanical seals of a double seal. Used to isolate the process fluid from the atmosphere. Also known as buffer fluid.
Base Plate:
The plate on which the pump and motor are mounted.
B.E.P:
Best Efficiency Point. The kinetic energy that a pump produces is never converted with 100% efficiency to pressure energy. There are always losses due to friction in the seals/bearings, friction of the pumped fluid over the impeller, etc,. The BEP is the volumetric flow rate of the pump for which the pump was designed to convert the most kinetic energy into pressure energy.
Bernoulli’s Law:
Describes the behaviour of fluid under varying conditions of flow and height. Formulated by Daniel Bernoulli is 1738.
B.H.P.:
Brake horsepower. The measure of an engine’s horsepower before the loss in power caused by any load (gearbox, etc.). Measured by attaching a “De Prony brake” to the engine’s shaft.
Bruna N:
Commonly known as Nitrile rubber. It is a synthetic rubber that is a co polymer between acrylonitrile and butadiene.
Canned Pump:
The armature, and shaft of the motor are in a can, used for pumping clean lubricating fluids.
Cantilevered Pump:
Centrifugal pumps often used in sump applications where it’s not desirable to have the bearings/motor under water. The impeller is at the end of a shaft which is cantilevered from the bearing housing assembly. Also known as an overhung pump.
Capacity:
The amount of liquid pumped per unit time. Measured in gallons/min, cubic meters per sec, etc.
Cartridge Seal:
An assembly containing the seal, gland sleeve and the rotating seal faces. Because it is self contained in can be installed without any measurement. Used in API seals.
Case:
The part of the pump that is the volute chamber, encloses the impeller(s). The case can be split radially or axially.
Cavitation:
Process in which small bubbles are formed and implode violently; occurs when NPSHa < NPSHr.
Check Valve:
A mechanical device that allows flow of a liquid in one direction only. A one-way valve that prevents fluid from flowing backwards in a pump.
Chopper pump:
A pump in which the impeller also acts as a cutting blade. Used with solid containing fluid applications to prevent pump blockage.
Close-Coupled pump:
A pump in which the impeller is mounted on the drive shaft. Close-couple pumps have the advantage of being compact, but are limited in size.
Closed or Open impeller:
In a closed impeller, the impeller vanes are contained within a shroud, causing the fluid to always be in contact with the impeller. An open impeller lacks this shroud. Closed impellers are more efficient, but can also clog easier if the process fluid contains solids.
Closed Impeller:
An impeller whose vanes are completely enclosed by two shrouds, one on the front and one on the back.
Colebrook equation:
In fluid mechanics, it’s important to understand the friction caused by interaction of the fluid with the internal surface of the pipe. The Colebrook (a.k.a. Colebrook and White) equation is one equation that can be used to calculate the friction factor of a fluid flowing in a pipe.
Condensate:
The fluid formed after a vapour has condensed. For example, water is a condensate of steam.
Coupling:
A connection between the pump shaft and the motor shaft. Can compensate for axial movement, but not radial misalignment.
Critical Speed:
The rotational speed at which acting dynamic forced cause a machine component (e.g. shaft, rotor) to vibrate at its natural frequency (also referred to as intrinsic frequency) and can even result in resonant vibrations throughout the entire machine and pump set. This effect has the potential to damage fast rotating machinery but can be minimised when such rotational speeds are passed through quickly.
Darcy-Weisbach equation:
An equation used for calculating the friction head loss for fluids in pipes, the friction factor f must be known and can be calculated by the Colebrook, the Swamee-Jain equations or the Mood diagram.
Dead head:
A dead head is a dangerous situation occurring when the pump is running but there is no discharge, either due to blockage in the line, or an inadvertently closed valve. The pump will continue to operate unit a safety shutoff pressure is reached. Prior to this, re circulation within the pump may cause overheating and damage to the pump.
Design Duty Point:
This is the point on a pump’s efficiency graph for the which the design has been optimised. It will be expressed as a particular capacity at a head or pressure of the process fluid. Ideally, this point should coincide with the pump’s best efficiency point.
Differential Pressure:
The differential pressure is the difference between the pressure of the system at the inlet and outlet of the pump.
D.I.N. Standard:
A standard published by the ‘Deutschese Institut für Normung” or German Institute for Standardisation.
Discharge Head:
The discharge head is the pressure at the discharge or outlet.
Double seal:
A pump with two mechanical seals on the drive shaft. Designed to prevent the process fluid from leaking. Used when pumping dangerous liquids that may have a tendency to crystallise or contain abrasive solids.
Dry Running:
Running a pump without any process fluid or without any lubricant for a seal.
Dynamic Head (system head):
The dynamic head is the component of the total dynamic head caused by friction in the system, due to interaction of the process fluid with the pipe walls.
End-suction pump:
End suction pumps are the most common type of centrifugal pump, they have a horizontal shaft with an overhung impeller and the flow goes in the end of the casing, and discharges from the top.
External Gear Pump:
A pump that uses gears to displace the process fluid. The gear or gears are housed in a casing with low clearance and one edge of the gear faces the inlet while the other faces the outlet. When the gear turns, liquid is trapped in the space between the teeth and it thereby moved from the inlet to the outlet.
Eye of the impeller:
The centre of the impeller, where the process fluid begins its journey outwards to the outlet or discharge.
First critical speed:
When increasing in velocity, it is the first speed at which the rotor bearing support system is in a state of resonance. The lowest speed that produces this resonance is the first critical speed. Subsequent increased speeds where this happens are known as the second, third, etc. critical speeds.
Flexible-coupled pump (Long coupled):
In contrast to the situation in a “close-coupled pump”, in a flexible coupled pump, the pump and driver each have separate shafts that are coupled through a flexible coupling.
Flooded Suction:
Liquid flows to pump inlet from an elevated source by means of gravity.
Flow:
A measure of the liquid volume capacity of a pump. Given in gallons per minute (GPM), litres per second and cubic metres per hour.
Flush:
Connecting an extraneous source of fluid to the pump’s stuffing box at a higher pressure than the operating pressure of the stuffing box. Can mix with and dilute the process fluid.
Foot Valve:
A valve that prevents loss of priming in centrifugal pumps when the source of process fluid is lower than the pump.
Friction Head:
The force (pressure) required to overcome the friction that is solely due to the inside of the pipes/fittings/pumps in a system.
Gasket:
A seal between static components in mechanics. Made of deform-able material.
Gauge Pressure:
The pressure exhibited on a dial gauge or on a digital read out from a pressure gauge. This reading indicates the pressure above atmospheric pressure and is usually measured in PSIG (pounds per square inch gauge).
Hastelloy “C”:
An alloy chiefly composed of nickel, molybdenum and chromium. Used in mechanical seals due to its corrosion resistance and insensitivity to halide stress corrosion.
Hazen-Williams equation:
Is an equation that relates the flow of water in a pipe to the properties of the pipe, and pressure differential caused by friction. Has been superseded by the Darcy-Weisbach and Colebrook equations.
Head:
A term in fluid mechanics to represent the energy stored in a fluid due to the pressure exerted on its container. Measured as a length f fluid where a standard of 10m is equal to one atmosphere.
Horizontal pump:
A pump where the rotating shaft is horizontal, as apposed to vertical.
Horse Power:
A measure of power, the rate at which work is done. One horsepower = 746 Watts. Initially adopted to compare the output of steam engines to the power of draft horses.
I.D.:
Inside diameter.
Impeller:
A device that attaches to a rotating shaft and converts the energy of motion, into the fluid being pumped.
Impeller eye:
The centre of an impeller and the point at which the liquid enters the impeller.
Impeller eye diameter:
The diameter of the opening where the fluid enters the impeller.
Impeller locating ring:
A ring concentric with the shaft that prevents the impeller from moving axially. Used to place the impeller on the shaft at the appropriate position.
Impeller nut:
A fastener, usually threaded and hexagonal that fastens the impeller to the shaft in overhung pumps.
Impeller setting:
Open impellers require a clearance between the discharge and the volute/back pump plate. It is necessary to set this clearance only after the pump reaches its normal operating temperature and must be reset to compensate for wear.
Impeller shroud:
A set of plates located on either side of the impeller vanes to prevent solids from entering and damaging the impeller.
Impeller vane:
A mechanical component of the impeller that directs the flow of liquid from the eye to the discharge, located at the out diameter of the impeller.
Inducer:
A small axial vane that is attached to the impeller to reduce the NPSH.
I.S.O.:
International Standards Organisation. Sets pump and seal standards for the community. Defines the popular ISO9000 standard for management.
Joule:
A unit of measurement of energy. Defined as the energy required to apply a force of one Newton through a distance of one metre.
Kilowatt:
One thousand watts. A watt is the SI unit of power, defined as one joule per second.
KPa:
An SI unit of measurement for pressure. Defined as one Newton per m2. 100kPa ~ one atmosphere.
KV:
Kilovolt or one thousand volts. SI unit of electrical potential difference. The difference that will impart one joule per coulomb of charge that passes through it.
L3 / D4:
A metric used to predict how well a pump will perform. L is the length of the shaft measured from the centre of the impeller to the centre of the radial or inboard bearing and D is the outside diameter of the solid shaft measured beneath the sleeve. For best performance, this number should be below 60 in imperial units and 2.0 in metric units.
Life Cycle Cost (LCC):
Life cycle cost is the total cost of the machinery including purchase, installation, operation, maintenance, repair and dispose of the machinery. Calculated when trying to decide whether to upgrade.
Lip Seal:
Also known as radial shaft seal. They are used to seal rotary elements such as a shaft or rotary bore.
Lobe pump:
Similar to gear pumps in operation, except that the lobes do not make contact. Positive displacement pumps that are popular where the sanitary quality is important.
Low Flow:
Must be taken into account when selecting a pump. Low flow can cause excessive heat build up in the volute.
Low NPSH pump:
A pump which has been designed to deal with a low Net Positive Suction Head. Prevents cavitation in the pump.
Magnetic Drive Pump:
A pump containing magnets within the impeller driven by a set of magnets mounted in a housing rotating on the motor shaft.
Mechanical seal:
A device that joins fluid-mechanical systems together by preventing leakage between the systems.
Minimum NPSHa:
The minimum net positive suction head available. The quantity should be larger than the NPSHr or the NPSH required.
Multistage pump:
Any pump with more than one impeller. Typically pumps with two impellers are referred to as two stage pumps.
Negative pressure:
In reference to any atmosphere. Anything less than this number is negative.
Newton:
The SI derived unit of force. Because force equals mass times acceleration, the Newton is equal to 1kg *m/s2.
Newtonian fluid:
A fluid that behaves without changing its viscosity as a function the rate of flow.
Non-Destructive Examinations(NDE):
A process which pumps or pump components are examines for defects without resulting in the destruction of the component being examined. A.K.A. Non-destructive testing (NDT).
Non lubricant:
In contrast to a lubricant, this type of fluid does not act to reduce friction of moving parts against each other.
Non-Newtonian liquid:
In contrast to a Newtonian fluid, this type of fluid has a viscosity that changes as a function of flow rate, or shear stress.
Normal operating point:
This is the set of conditions at which the pump normally operates. It could be the same or different than the best efficiency point or the rated operating point.
N.P.S.H.a:
The net positive suction head available that can be used to prevent cavitation within the pump. It is defined as static head plus surface pressure head minus the vapour pressure of the process fluid minus the friction loss due to the piping, valves and fittings.
N.P.S.H.r:
Net positive suction head required to keep a pump from cavitating. A characteristic of the pump. Calculated by the manufacturer with cold water.
Open Impeller:
An impeller with vanes attached to the hub with no front or back shrouds; the impeller may have small web in-between vanes for structural support.
Over hung impeller:
An impeller on a shaft that is supported on one side only.
Pascal:
The SI derived unit of pressure. Equivalent to one Newton/m2. 1 atmosphere of pressure is equal to a little over 100KPa.
P.D. Pump:
Positive displacement pump. This causes a fluid to move by trapping a fixed amount of the fluid and moving it into the discharge pipe. Pumps up to very high pressure, but low flow rates.
Performance Curve:
A graph depicting the plot of total head vs flow rate for a specific pump, with a specific impeller and set of characteristics.
Peripheral (regenerative) pump:
Also known as regenerative or regenerative turbine pump. An alternative design to a centrifugal pump. In these, fluid passes through the vanes many time (instead of once, in a centrifugal pump). The impeller has short vanes at the periphery and these vanes pass through a ring shaped channel. The fluid enters between two impeller vanes and is set into a circular motion, this adds energy to the fluid particles which travel in a spiral like path from the inlet to the outlet. Each set of vanes continuously adds energy to the fluid particle.
Peripheral speed:
The velocity, or speed, at the periphery of some diameter.
pH:
The measure of how many H* ions or OH ions are in solution. The scaled is logarithmic and ranges for 0 (very acidic) to 14 (very alkaline).
Pipe friction loss:
The loss in head due to the friction between the process fluid and the walls of the pipes and joints.
Pipe roughness:
A measurement of how rough the inside surface of a pipe system is. Many measurements are taken and averaged. It is the average size of peaks that are on the internal surface of the pipes producing friction.
Positive displacement pump:
A type of pump that causes a fluid to move by trapping a fixed amount of the fluid and moving it into the discharge pipe.
Power factor:
In an AC circuit, the relationship between the real power flowing to the load and the apparent power in the circuit.
Pressure:
The force exerted on the walls of a tank, pipe, etc. by a liquid. Normally measured in pounds per square inch (psi) or kilopascals (kpa).
Pressure drop:
The difference in pressure between two areas of a pump, or between the inside and outside of a container.
Pressure head:
The pressure at the pump exerted by atmospheric and other additional pressure that might be in the vessel.
Prime:
In a centrifugal pump, if the source is lower than the pump, a small amount of process fluid is infused into the pump to start the suction process.
Progressive cavity pump:
A positive displacement pump. Ideal for fluids with high viscosity (e.g. grease, pastes, etc.) They are also known as eccentric screw pumps.
Q:
Commonly used as a symbol for flow rate (quantity). Units may be expressed as any volume per unit time.
Quench:
Adding fluid outside the seal to either cool the seal, or to dilute any product leaking out of the seal face.
Recessed impeller pump:
Sometimes known as vortex pump. A pump design which reduces contact between the impeller and process fluid by recessing the impeller. Ideal for slurries containing solids or fibres.
Relative density also known as Specific gravity (S.G)
Ratio of a liquids density to that of water measured at 4°C.
Reynolds number:
A dimensionless number that relates the ratio of inertial forces (velocity) to viscous forces.
Self/Dry Priming:
Draws liquid up from below pump inlet (Suction lift), as apposed to pumps requiring flooded suction.
Semi-Open impeller:
An impeller with no front (Suction) shroud. Used typically when pumping particle containing fluids.
Shaft:
The component of the pump that transmits the radial force from the motor to the impeller.
Shaft flexibility factor (SFF):
A dimensionless number, characterising the relative stiffness of a shaft or rotor. Using the formula SSF = (L3 ) / (D4) will calculate SFF. Where L is the length of the shaft and D is the diameter. Can be used to compare shafts.
Shaft packing:
Seals are expensive, so manufacturers supply their pumps with soft packing to seal the shaft. Mechanical seals then replace the shaft packing.
Shaft sleeve:
A thin cylindrical, metal or plastic sleeve placed around the shaft to prevent wear and tear.
Shore “A”:
A scale used to measure hardness of materials. Defined by Albert Shore in the 1920s.
Shut-off head:
The shut off head is the head pressure) delivered by the pump with the discharge valve closed (shut off).
SiC:
Silicon carbide. Very hard and durable, therefore commonly found in seal faces.
Single stage pump:
A pump with a single impeller. Compare to two-stage and multistage pumps.
Single suction pump:
A pump with a single suction impeller, either the first impeller in a multi-stage pump or the only impeller in a single stage pump.
Slurry:
A mixture of liquid and solid.
Slurry pump:
A heavy duty pump designed to withstand the corrosive or abrasive effects of particles in the process fluid. Achieved by lining the pump with extra material that can withstand the assault.
Specific Gravity:
Ratio of a liquids density to that of water measured at 4°C. Pumping heavy liquids (specific gravity greater than 1.0) will require more power.
Specific speed:
A dimensionless number user to characterise turbo machinery. Normalises impellers to a speed in revolutions per minute to that of a geometrically similar impeller if it were to deliver 1 gallon per minute against 1 foot of hydraulic head.
Strainer:
A devise installed in the inlet of a pump to prevent foreign particles from damaging the internal parts.
Submersible pump:
A pump that operated when it is completely submerged. Must have waterproof electrical circuits and is usually liquid cooled.
Suction bell:
A bell shaped tubular section at the inlet of a vertical pump. Used for directing the flow of liquid into the impeller inlet.
Suction head:
Suction head is the term for the head due to the fact that the source of the pump is above its centreline.
Suction lift:
Opposite of suction head. Occurs when the source is below the pump’s centreline.
Suction specific speed:
A number that will determine what type of geometry to use for maximum efficiency, but prevent cavitation.
Suction Static Head:
The height difference between the surface of the inlet reservoir and the centreline of the pump. If the tank is pressurised, this pressure is also included.
Suction Static Lift:
AKA. suctions static head. Only occurs when the pump is above the inlet reservoir.
System Curve:
A graph depicting the pump’s total head vs flow. It is used to estimate performance at different flow rates. The total head includes the static head (constant) and the friction head and velocity head different – and these depend on the flow rate. The intersection of the system curve with the pump characteristic curve defines the operating point.
Sump:
A well or pit in which liquids collect below floor level; sometimes refers to an oil or water reservoir.
System head:
The head (pressure) cause by friction along the pipe walls and due to the joints in the system.
Thermoplastic:
A plastic material that can be melted over and over again without changing its properties. Used in injection moulded plastics.
Thermosetting:
Unlike a thermoplastic, this material can only be melted ones and after it has cooled and set, it cannot be re-melted without losing its properties.
Thixotrophic fluid:
A fluid whose viscosity decreased with agitation. e.g. non-drip paint.
Total Dynamic Head:
This term has been replaced by and is equivalent to “Total Head”.
Total Head:
The sum of the head produced by the pump. It can be calculated by subtracting the suction head from the discharge head.
Underfile, or underfiling:
Changing the impeller vanes by hand grinding some metal off of them. This will change the pump’s performance by reducing the vane thickness and increasing the area of opening between adjacent vanes.
Vane pump (hydraulic):
A positive displacement pump that consists of vanes mounted on a circular rotor. The rotor sits inside a circular cavity and the two circles are offset, to create eccentricity.
Venturi (Bernoulli’s law):
A pipe that has a section in its middle of smaller diameter than either end. The pressure in this area will be less than the pressure in the area of piping with the larger diameter.
Vertical pump:
Any pump where the shaft is mounted vertically.
Viscosity:
Describes the internal friction of a moving fluid. A fluid with high viscosity (E.g. paint) resists motion because it molecular makeup causes internal friction whereas a low viscosity liquid (e.g. water) flows easily because its molecular makeup results in very little friction when in motion.
Vortex pump:
Used in an application where a very large percentage of solids are contained within the fluid, it operates by having a recessed impeller that is out of the flow path.
Water hammer:
Occurs in a piping system due to rapid fluctuations in pressure. Usually caused by change in pump condition, or the opening or closing of a valve too rapidly.
Watt:
A measure of work. The rate at which work is done when an object’s velocity is held constant against an apposing force of one Newton. (Units are Newton meters/second.)
Wet end:
The components of the pump that get wet from pumping the fluid. Stuffing box, impeller, volute, etc.