View Our Range
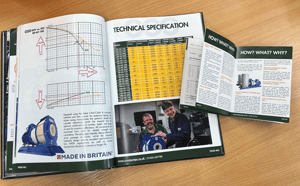
Browse Our Resources
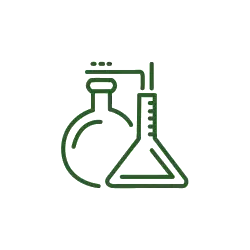
View Now
Chemical Compatibility Table
Quickly check which pump materials are compatible with thousands of chemicals and corrosive substances.
View Now
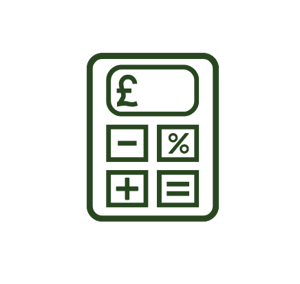
Read More
Lifecycle Cost Calculator
Calculate the true cost of your pump investment — including energy, maintenance, and downtime — not just the purchase price.
Read More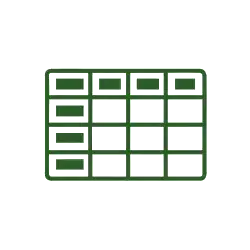
View Now
Conversion TablesAccess useful engineering conversions for flow rate, pressure, temperature, and more — all in one place.View Now
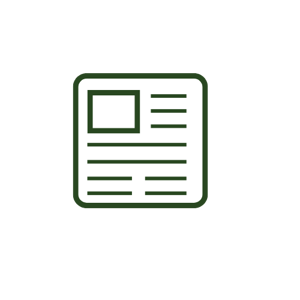
Read More
Blog
Insights, tips, and updates on chemical pumps, efficiency, regulations, and smart engineering decisions.
Read More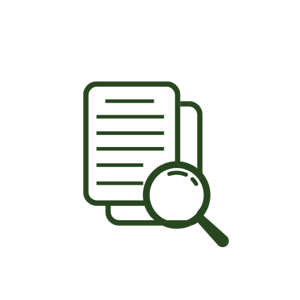
Read More
Case StudiesReal-world examples of how Crest Pumps solved tough process challenges for customers across industries.Read More
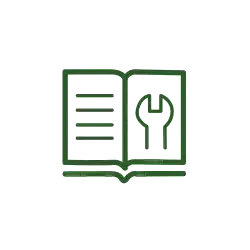
View Now
Atex GuideUnderstand ATEX zones and explosion protection requirements for safe pump selection in hazardous environments.View Now

Read More
Crest NewsCompany updates, product launches, team news, and behind-the-scenes stories from Crest Pumps. Read More
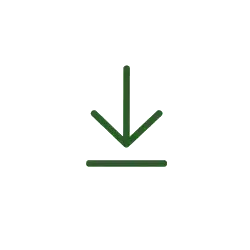
View Now
DownloadsFind brochures, datasheets, manuals, and technical documents for our full pump range — ready to download.View Now
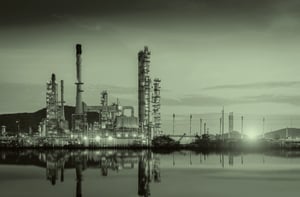
THE CREST PUMPS LIFETIME GUARANTEE
No matter how old your pump becomes, in the unlikely scenario that you have a problem, our engineers will be on hand to diagnose the issue and help you get up and running again.That’s why, with Crest Pumps you’ll never need to worry about unplanned downtime again.
Talk to us now to discuss your chemical pump requirements or book a free site audit to see how much time and money you could save!
Trusted By The Best
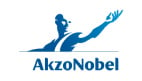
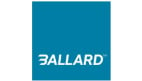
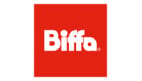
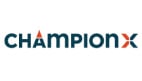
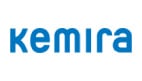

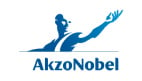
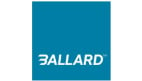
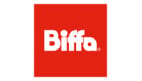
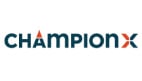
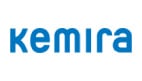

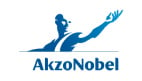
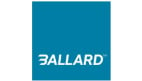
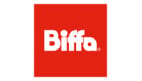
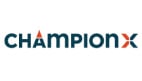
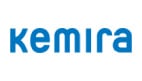

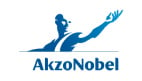
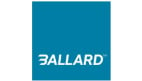
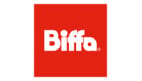
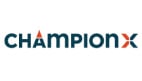
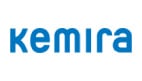

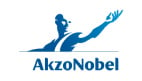
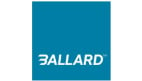
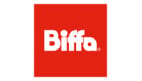
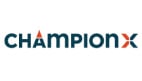
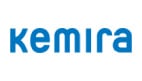
