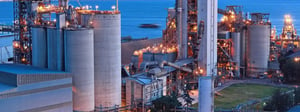
How to ensure a long life for your mechanical seal
Mechanical seals continue to be the number one cause of chemical pump downtime.
This is normally because the seal face has either worn out or the seal has suffered damage. If it’s the former, replacing the mechanical seal is normally the logical course of action. But if it is the latter, it’s likely the rest of the system will need investigating in order to diagnose the true cause of the problem.
The above diagram shows the high rate of seal failures compared to other components of pumps. On a damaged shaft seal, it is normally possible to observe the cause of the damage, by the application of the pump. Then record this information in a damage report, including the details of the operating conditions.
Vibration
Pump systems are prone to vibrations, from any different source. Operation of a pump away from its BEP (Best Efficiency Point) on the pump curve can cause cavitation. Which can be the source of vibration transmitted through the impeller to the mechanical seal. When using variable frequency drives, allow the pump to operate near its critical speeds can be fatal for the pump as high speeds can produce large scale vibration.
Regardless of the source, vibration in a pump system is the misalignment of the coupling or suction. Some of the most common failure modes are;
- Breakdown of the lubricating film stiffness between the seal faces that result in face wear and chipping.
- Fatigue failure of the welds in a metal bellows seal.
- Wear of the drive mechanism. This includes the pins, lug and mating slots, grooves and holes resulting in the loss of axial tracking and damage to the seal rings.
- Loosening of the drive collar set screws, causing a loss of the torque transmission on the rotating components.
Lubrication failure
The seal face lubrication is a critical requirement for a mechanical seal to function within a pump system. Wet contacting mechanical seals rely on the existence of a fluid film between the seal faces. This minimises wear and friction and provides a reliable performance.
If a pump operates away from its BEP, then this can cause loss of fluid to the fluid film, leading to face to face contact that results in high friction, increase temperature and accelerated wear. The seal will degrade and then fatally fail.
A way to maintain your pump, to ensure that it will not dry run is to install a Dry Run Monitor. This stops any chance of your centrifugal pump from causing unnecessary downtime. The Dry run monitor is provided with an alarm setting which alerts the user to know there is an issue with the pipework. And there isn’t sufficient fluid within the system by monitoring the percentage the level of amps.
Alternatively, you use a dual seal system. Two sets of seal faces are installed as an enclosed unit, containing its own circulating fluid, with the lubrication inside the dual seal. This means that the contaminated fluid cannot leak into the seal, leaving it only cool, clean and compatible for lubricating the seal faces.
The best way to ensure a long service life for your seal, is to lubricate them with cool, clean and stable fluids. However their dynamic nature makes them the first thing to fail if something else in the system fails. Vibration, dry-running, pump misuse and miss-installation can all cause the seal to fail.
Therefore it is paramount to have routine maintenance to ensure the pump is fully operational and at the BEP. And only then can you ensure a full working life with your chemical pump.
If you have a particular enquiry, please email us and we will be delighted to help.
Find us on Socials
We regularly update our LinkedIn page with articles and news, so go give us a follow to stay up to date.