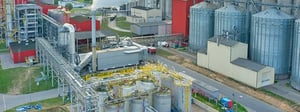
What are the most efficient and reliable pumps for Biofuel plants?
- Demands for efficient and reliable pumps for biofuel plants has grown in the last five years
- Safety and consistency are of paramount importance for hazardous biofuel processes
- Biofuel pumps can be tailored to your plant’s specifications
- Seal-less leak -free magnetic drive pumps are built for high efficiency in biofuel industries
- Case studies show the use of pumps in biofuel scenarios
With the growing demand for pumps used in biofuel installations, Crest Pumps has been a market leader in providing safe and consistent pumps for biofuel plants.
We aim for safety because of its paramount importance in this often volatile environment, even building pump solutions tailored to your plant’s specifications, making sure your individual solution is exactly right for your process.
Using seal-less, leak-free magnetic drive pumps built in a range of durable and corrosion resistant materials achieves a high efficiency rating that will increase the lifespan of your pump.
Crest’s pump range has been used in Biofuel tank loading/unloading, plant transfer, biofuel mixing and biofuel storage; and is also ATEX certified for explosive environments.
Crest has worked with many companies in the biofuel industry, including a waste to energy plant in Oldsbury for Chinook Sciences; as part of the pasteurisation process of a food recycling programme for Agrivert Ltd.; and processing bio-fertilizer and methane gas from organic waste for Fernbrook Bio.
Contact our helpful and expert engineers to discuss your Biofuel plant pump requirements on 01425 627700 or get in touch via our enquiry form
We often post articles and other news on our LinkedIn page. Go and follow to keep up to date, or for any pump queries you may have please contact us.